Plastic barrel blow molding process outlined
Blow fundamentally plastic bucket can be divided into two categories: extrusion - blow molding and injection - blow molding. The main difference between the two lies in the preparation of the parison and then blow the same fundamental process. Unfolded at the foundation of these two approaches are forming: Extrusion - stretch - blow molding (referred to squeeze - pull - blow), injection - stretch - blow molding (referred NOTE - pulling - blowing) and multi-enantiomer plastic and so on. Injection - blow molding (referred NOTE - blowing) plastic bottles is the use of the first plastic injection molding the bottomed parison and then the parison is hot to move the blow mold blow molded hollow articles. NOTE - Blow container does not flash, good dimensional stability, excellent bottle and thread quality, parison thickness can be pre-conditioning, good products gloss, thriftiness materials. But note - blow molding inappropriate consumption of large and complex shape of the container, but also due to the use of two pairs of injection and blow molds, so a large investment in equipment. NOTE - Blow bottle shape container with small single-cylinder-based, it can be used polyvinyl chloride, polyethylene, polypropylene and polystyrene, polyester, polyamide, and other resin consumption. The type of plastic packaging mainly used for medicine, food, cosmetics, etc. for blow molding of polyethylene, polyvinyl chloride, polypropylene, polystyrene, linear polyesters, polycarbonates, polyamides, cellulose acetate and polyacetal resin or the like. Which takes account for the first high-density polyethylene. It is widely used in food, chemicals and disposal of liquid packaging. High molecular weight polyethylene suitable for the manufacture of large fuel Cuo tanks and barrels. PVC due to better transparency and tightness, so get widely used in packaging cosmetics and washing agents. With non-toxic PVC resin and additives development, and stretch blow molding technology to carry out, the amount of PVC in food packaging container of the rapid growth and has begun for beer and other beverages containing carbon dioxide gas package. Linear polyester materials in recent years into the category of the new blow molding materials. Because of its products have glossy appearance, excellent transparency, high mechanical strength and better storage container goods, environmental and other aspects of the advantages of no pollution when burning waste disposal, so soon carry bottles, particularly pressure plastic food containers used in the most general terms. Its progress modified polypropylene resins and processing technologies, the use of volume also increased year by year. The main raw materials and typical formula (l) polyethylene generally used in a melt index of 6 l ~ polyethylene resin. (2) common network selection polypropylene melt index of 2-4 polypropylene resin. (3) Common use general-purpose polystyrene or impact polystyrene resin injection type.
(4) Hard transparent PVC bottle formulation. Plastic barrels of production of major equipment and characteristics (1) extruders and extrusion head and ordinary - Equipment blowing Fundamental same. (2) the disposal of the parison extruder installed by tubular parison, to go through the installation stops cutting, bottom and neck fusion process to produce test-tube-shaped bottomed parison. (3) The preform is heated preform heating installation equipped with multiple, heating oven, heating sleeve, heating channel, etc. can be electrically heated or infrared heating. But the heating installation to be able to balance the thermostat and heating, the temperature difference between inside and outside the parison to minimize. (4) Tensile stretching mandrel are mounted and two kinds of stretching jig. ① stretch stretching mandrel mandrel inserted from the upper portion of the parison in the hydraulic action against the type of bottom blanks, stop longitudinally stretched, then the pores on the mandrel into the compressed air blown through, stop radial stretch. Most stretch forming are using this stretching installation. ② stretching jig jig to stretch both ends of the tubular parison from an external folder, stop longitudinally stretched at a hydraulic effect, then stop the radial stretch blow. Neck and bottom trimmed demand has burrs, burr crushed recyclable applications. (5) squeeze - pull - Blow molding machine abroad a variety of types and sizes crowded - pull - Blow molding machine, currently there is no domestic production of this special equipment plastic bucket craft Note - blowing by injection molding practice parison and blow molding products of two processes, and injection molding the parison is key to the whole process of consumption
(1) injection molded preform injection temperature process control ① injection temperature and the type and thickness of the article and other elements of the type and characteristics of raw materials, injection molding machine related. Of crystalline resin, such as polyethylene, polypropylene and the like, the injection temperature should be above its melting point. Amorphous polymers such as polystyrene, polyvinyl chloride, injection temperature is higher than the temperature of viscous flow thereof. Melt the low number of batches of resin melt index higher than a resin injection temperature is higher. Use of a plunger-type injection molding machine than the screw injection molding machine processing temperature is higher. Thin wall parison than the thick preform injection temperature of the high demand. Ordinary polystyrene injection temperature of 140 ℃ ~ 240 ℃, polyethylene 150 ℃ ~ 280 ℃, polypropylene 205 ℃ ~ 285 ℃, PVC is 160 ℃ ~ 190 ℃. Ordinary injection mold temperature is 40 ℃ ~ 80 ℃. ② ordinary resin injection pressure of the melt index is low, the parison wall is thin, high injection pressure request, otherwise low. Plunger injection molding machine is higher than the pressure screw injection molding machine needs. In ensuring product quality situation, as far as possible the use of lower injection pressures. Ordinary polystyrene injection pressure 58.8 ~ 107.9MPa, polyethylene 58.8 ~ 98.06MPa, polypropylene 54.9 ~ 98.06MPa, PVC is 78.4 ~ 127.5MPa. (2) Control and extrusion blow molding process - a fundamental blow molding process blow molding same. Major equipment and characteristics (1) the structure of the parison injection machine and the ordinary injection molding machine simply the same, but lower injection pressure, screw length may be smaller, the compression ratio should not be too large. (2) mold including injection mold and blow mold. Parison injection mold and ordinary injection mold fundamental data and processing the same request, but must be a hollow mandrel to pass into the compressed air. Blow molds and extrusion - blow molding die simply different. (3) Installation and squeeze release - Different blow molding, blow molding process after completion of the blow mold open, the molded article with the mandrel to the stripping installation, by a stripper plate will separate article and mandrel. Product specification - injection blow-molded plastic bottles are currently no national standard and the Ministry of standard, product specification may refer polyethylene blow barrels specification, and make the necessary corrections. But the same kind of material NOTE - Blow container than crowded - Excellent Blow container properties. 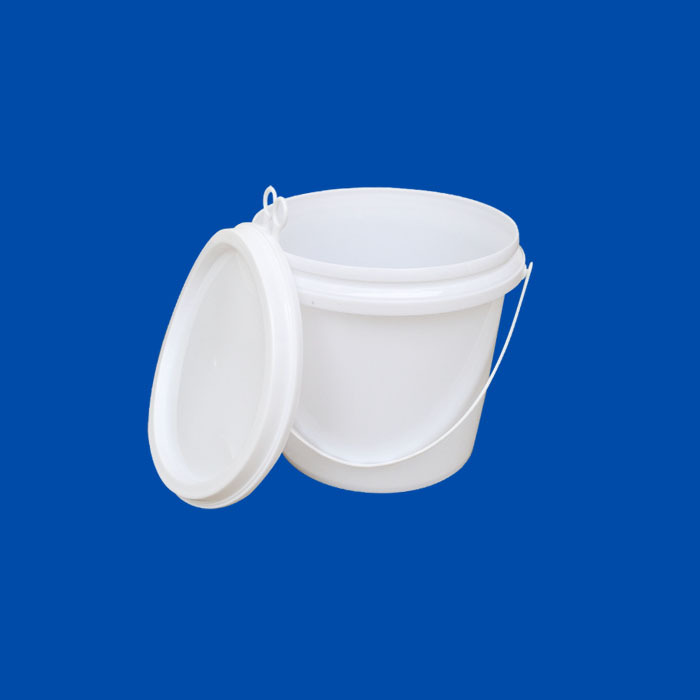
|
|